A solid spine is what gives strength and stability.
It´s also a carrier of courage and confidence, which is much needed in order to take the lead in reducing the environmental footprint of our industry.
Green Spine Line® playlist.
Paving the way for sustainable construction with Green Spine Line®
All across Europe, Consolis is tackling the climate challenge head-on, with deeds, not just words. Our low-carbon solution, the Green Spine Line®, now accounts for 38 percent of our total production as of 2024. This milestone marks the beginning of our steadfast commitment to revolutionizing the construction industry and fostering sustainable local communities.
Since its introduction, the Green Spine Line® has experienced continuous growth, underscoring Consolis’ dedication to leading the charge towards sustainability. Its availability across multiple markets demonstrates our readiness to provide customers with innovative, climate-smart solutions.
Alternative binders to minimize cement:
- In the Netherlands, we are testing calcinated clay.
- In Sweden, we started using husk ashes.
- In Denmark, we are using a new type of fly ash,
where a major part of the material is biobased.
Strategic partnerships:
- In Finland, we have introduced an entire low-carbon product line. In the case of YIT, a major customer, the switch from hollow core slabs to a low-carbon version means a reduction in CO2 emissions of 4,000 tons per year.
- In Spain, we have partnered with climate-tech pioneers CarbonCure Technologies to reduce carbon emissions.
Reducing the climate impact is one of the most important challenges we, and the whole building material industry are facing. At Consolis, we are determined to take the lead in the sustainable transformation of our industry, with the goal of being climate neutral by year 2050.
We approach this challenge head-on with one of our concrete measures being the introduction of Consolis Green Spine Line® – certified and sustainable precast products, solutions and methods.
Precast concrete is the building material of the future. It is flexible and versatile, cost effective and it has extremely long durability.
The challenge is to reduce climate impact of the production, an area where we currently are taking giant leaps in the right direction.
Our holistic and outside-the-box approach include recipe optimization, smart design, industrial production, reuse of elements, recycling of material and strategic partnerships with our customers, the industry and academia.
We call the result of our efforts Green Spine Line® – a certified product line that will help our customers make a real difference in their journey towards CO2 neutrality. The market demands it, and our planet needs it.
Certification - forerunning the market
Creating common standards on a global market is complicated and takes time. We respect that process, but we won’t let it slow down our own ambitions to be forerunners and to show what’s possible. Consequently, we have created our own certification criteria for the Green Spine Line®.
Certification criteria:
- Market Leadership: At least 15% lower CO2 emissions compared to precast industry standards. That in turn means at least 60% lower than comparable in-situ concrete.
- Continuous Improvement: A clear plan and local commitment to continuously reduce the CO2 emission of the components even further over time.
- Customer Significance: The products must have the commercial power to make a significant impact on our customers journey towards CO2 neutrality.
Certification steps:
- Products are confirmed locally to be applicable for Consolis Green Spine Line® certification, i.e all criterias are fulfilled.
- The request is put forward to Consolis Group Sustainability Management Committee.
- A review is made to confirm or decline.
- Consolis Executive Management Team via its Group Sustainability Committee confirm the certification and gives approval for sales and marketing of the new Green Spine Line® product.
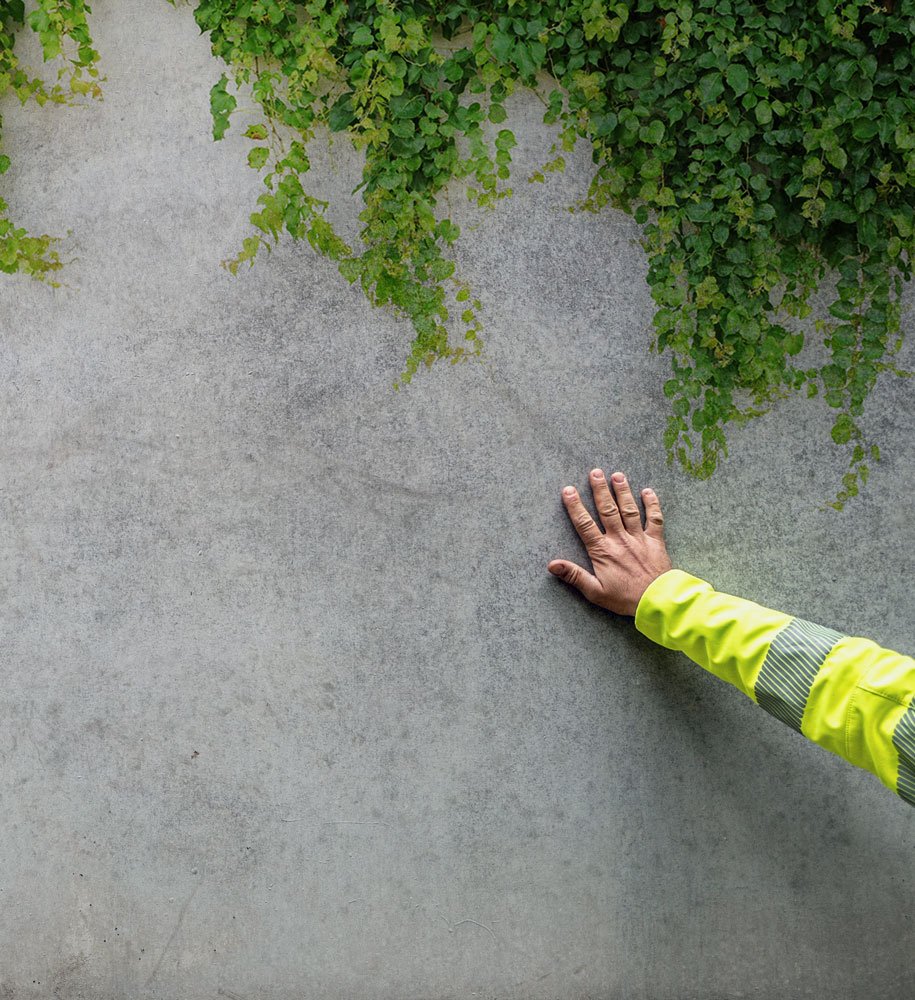
Products
Consolis offers several products fulfilling the Green Spine Line®.
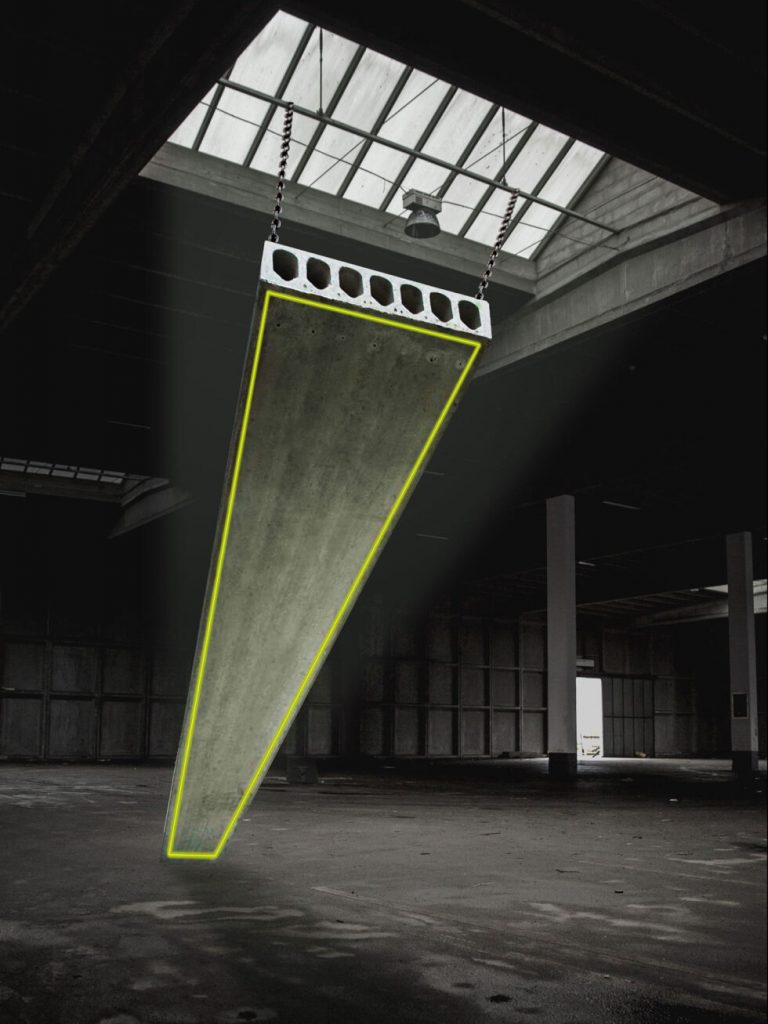
Green Hollow cores
A key product is our Green Hollow core slabs, basically the floors and the ceilings of a precast frame. The Hollow core slabs have many advantages and can be used for many different purposes. One of the best fits is to use it for flooring: it is slim and light thanks to its hollow ‘channels’. But at the same time the slab is strong and can carry heavy loads. Its size and weight also makes it possible to cast, load and transport more slabs, saving both time, resources and energy. They can also be varied depending on intended function.
As of now we can offer Green hollow cores in Finland, Sweden, Norway, Denmark and in the Netherlands. With 40% lower CO2 -emissions in Finland and 19% lower CO2 -emissions in Sweden compared to industry standard, our hollow cores can truly make a difference. We’re now pushing the pace to make green hollow core slabs available on more markets.
Green Walls
In Finland, Spain, Sweden and Estonia we can offer Green walls, significantly reducing the CO2 -emissions of construction projects.
For example, CO2 -emissions from producing the frame of a concrete-structured apartment building can be reduced by up to a third by using low-carbon wall elements. Our Green walls are initially available for partition and inner shell structures, but we are continuously developing new Green products.
Green Columns and Green Beams
In Spain in addition to Green Walls we offer Green Columns and Green Beams. These Green Beams – prestressed horizontal structures – have about 13% CO2 reduction.
Staircase
In Sweden, a staircase with 30% reduced carbon dioxide emissions is the latest addition to Consolis’ Green Spine Line®. Now available in Sweden through Consolis Strängbetong, this staircase is made with climate-improved concrete and emits only 135 kgCO2e/tonne, in line with Svensk Betong’s (Swedish Concrete Federation) Climate-Improved Step 3.
Green Hollow cores
A key product is our Green Hollow core slabs, basically the floors and the ceilings of a precast frame. The Hollow core slabs have many advantages and can be used for many different purposes. One of the best fits is to use it for flooring: it is slim and light thanks to its hollow ‘channels’. But at the same time the slab is strong and can carry heavy loads. Its size and weight also makes it possible to cast, load and transport more slabs, saving both time, resources and energy. They can also be varied depending on intended function.
As of now we can offer Green hollow cores in Finland, Sweden, Norway, Denmark and in the Netherlands. With 40% lower CO2 -emissions in Finland and 19% lower CO2 -emissions in Sweden compared to industry standard, our hollow cores can truly make a difference. We’re now pushing the pace to make green hollow core slabs available on more markets.
Green Columns and Green Beams
In Spain in addition to Green Walls we offer Green Columns and Green Beams. These Green Beams – prestressed horizontal structures – have about 13% CO2 reduction.
Green Walls
In Finland, Spain and Sweden we can offer Green walls, significantly reducing the CO2 -emissions of construction projects.
For example, CO2 -emissions from producing the frame of a concrete-structured apartment building can be reduced by up to a third by using low-carbon wall elements. Our Green walls are initially available for partition and inner shell structures, but we are continuously developing new Green products.
Staircase
In Sweden, a staircase with 30% reduced carbon dioxide emissions is the latest addition to Consolis’ Green Spine Line®. Now available in Sweden through Consolis Strängbetong, this staircase is made with climate-improved concrete and emits only 135 kgCO2e/tonne, in line with Svensk Betong’s (They have an english name) Climate-Improved Step 3.
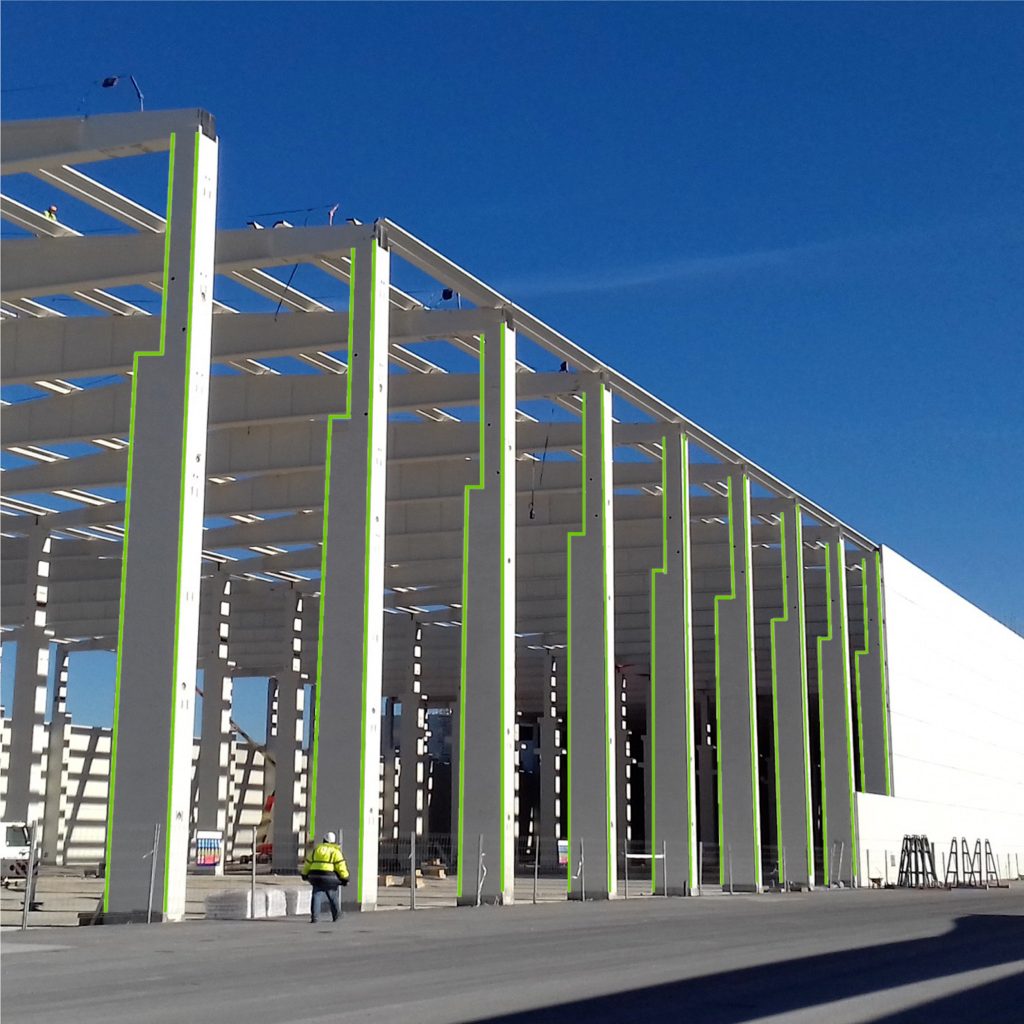
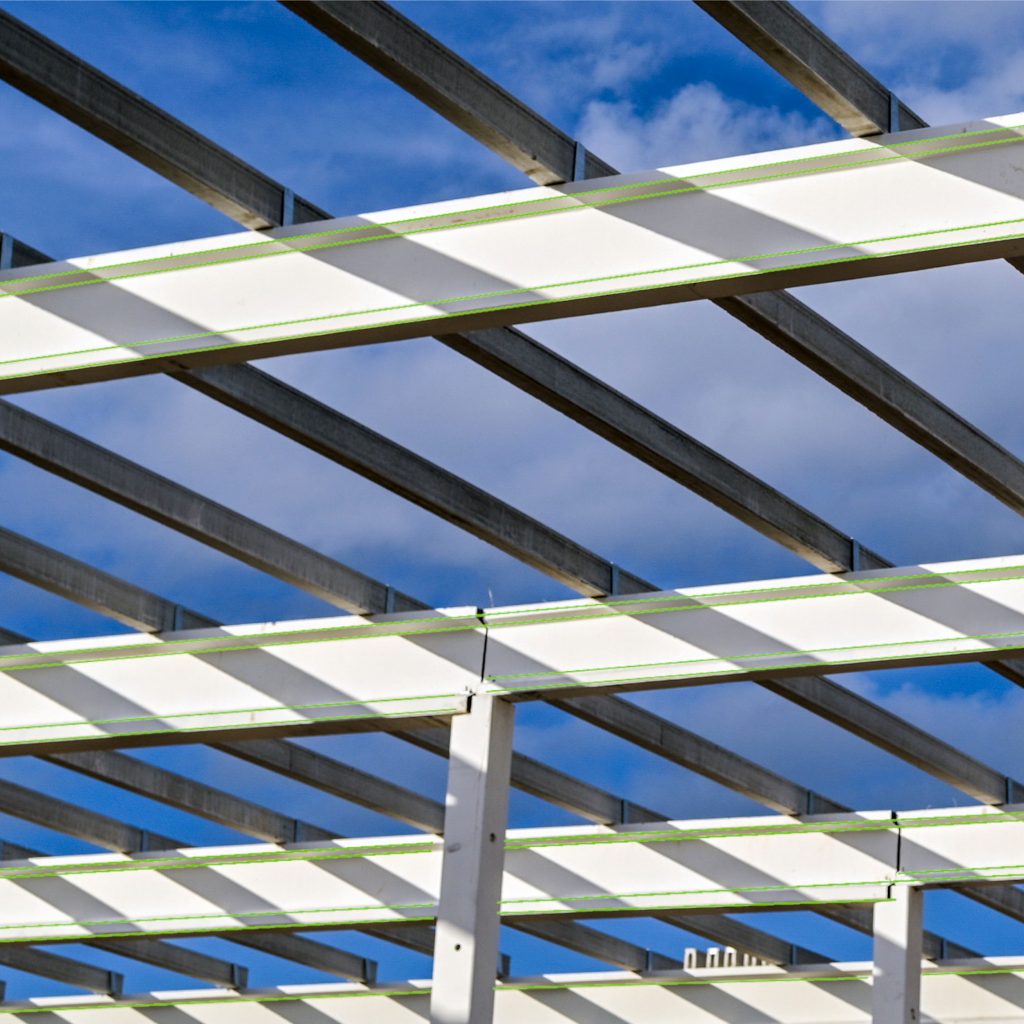
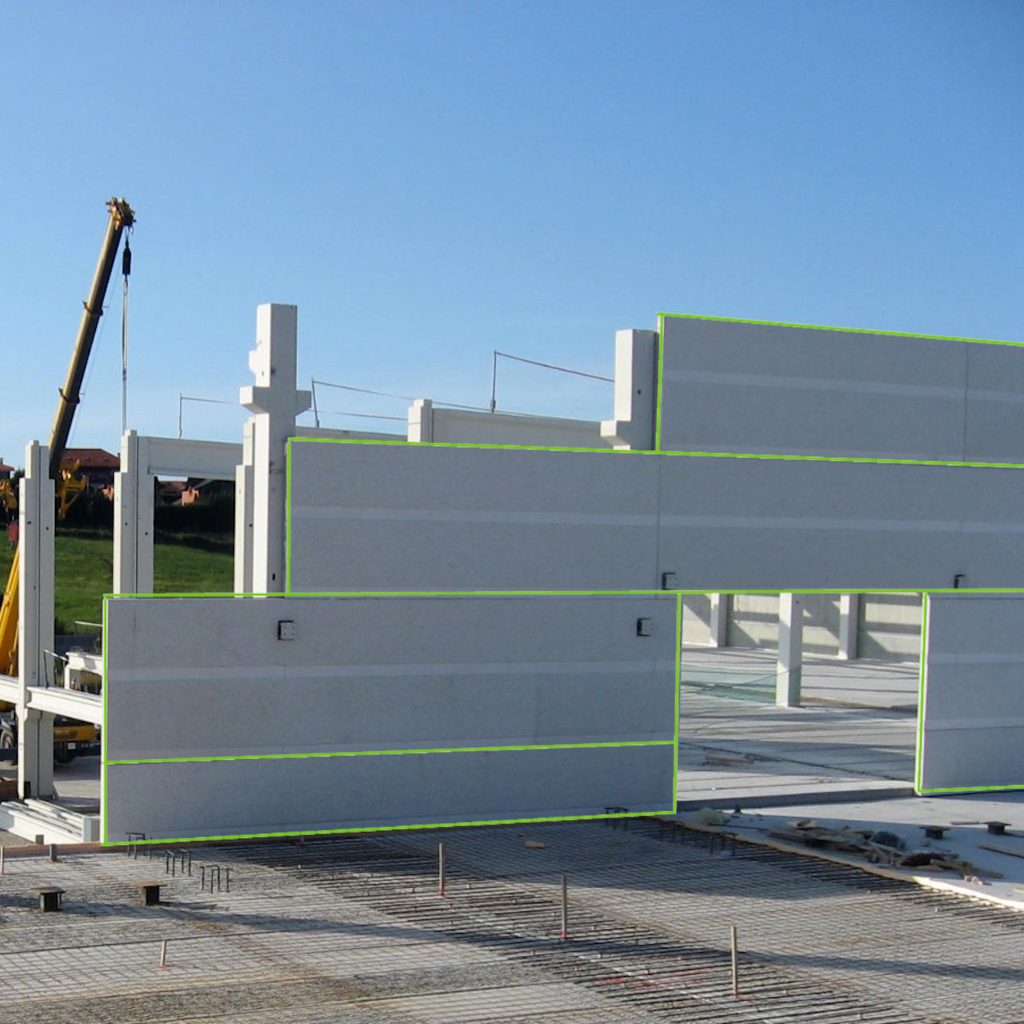
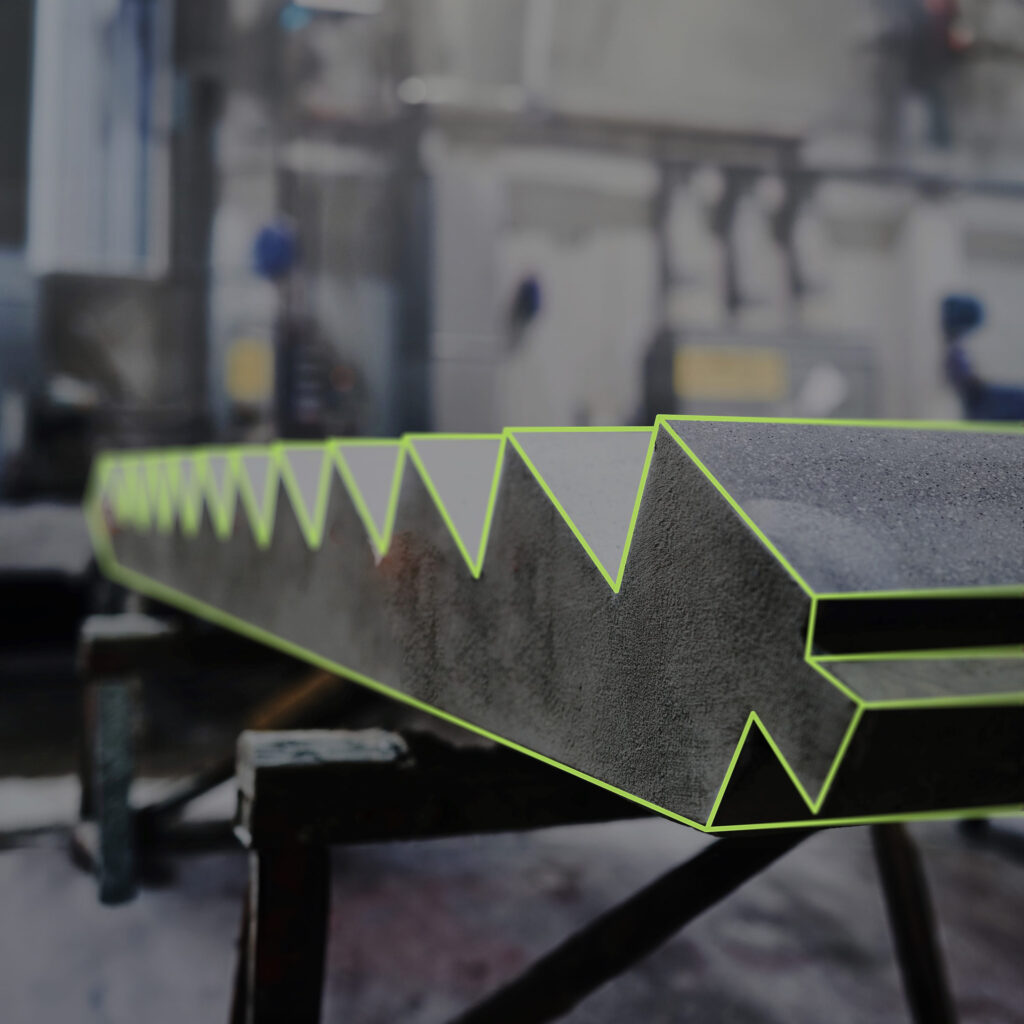
Future products
In our Green pipeline we have many more products to come. We are starting with the above products, but aim to add other elements. Our plan is to keep expanding the Green Spine Line® in a majority of our markets. We have picked up speed and we keep accelerating toward our goal; To provide the spine for useful, long-lasting buildings and to be the forerunner in the sustainable transformation.
Methods
To reduce our climate footprint we have taken a number of measures in our production. Below is a brief introduction to the most important ones and why they make a difference.
Green ingredients
Cement is the single most CO2 -emitting ingredient in concrete and our main focus is to reduce the need of cement.
On our local markets we are working with a range of disruptive players with the aim of finding new smart ways of producing concrete.
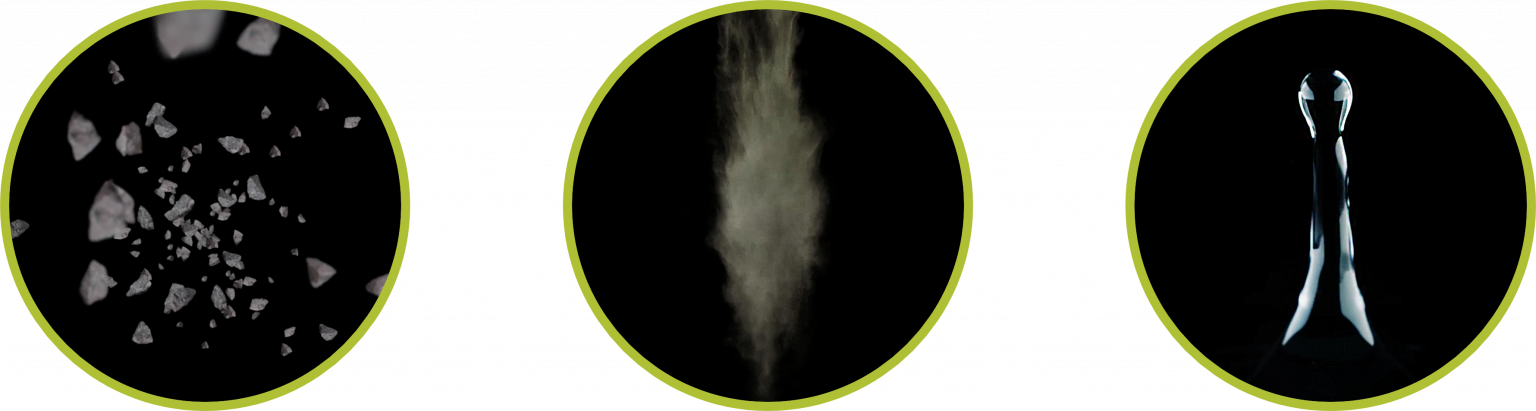
Already today we add alternative binders to the mix, such as flyash a rest product from the energy industry and slag, a rest product from the steel industry. We also experiment with other binders, for example clay and husk ashes from rice and grain.
For many years already, we have had alternative top quality concrete recipes in use in our Nordic markets. The new recipes contain an increased proportion of slag and reused concrete. The water-cement ratio has been increased from VCT 0.40 to 0.45, which means more water and less cement.
Green design
Our hollow core slabs is a great example of how design is a vital tool in the sustainability process. In short, we make more out of less by producing slimmer and lighter products without affecting their performance.
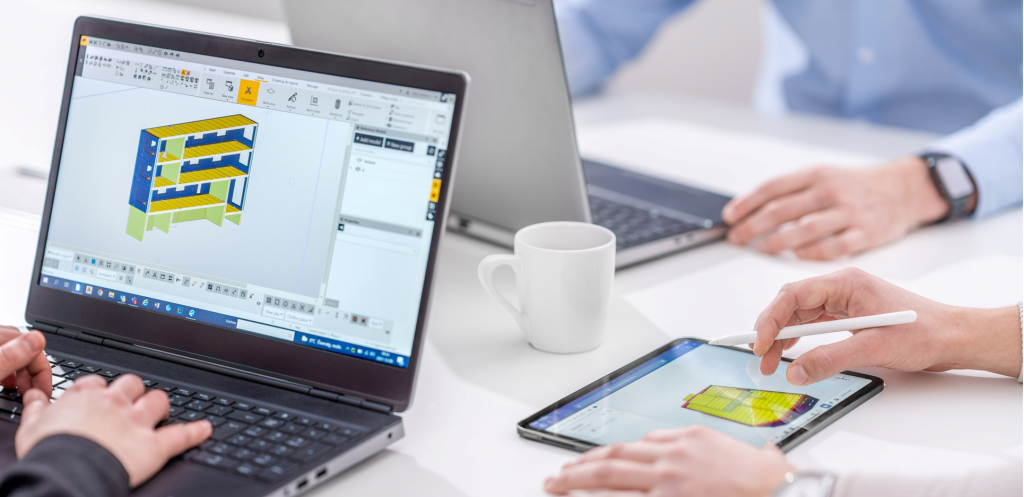
Another crucial design feature is to design beyond the buildings first intended area of use.
Today buildings and entire neighborhoods are often monofunctional which means they are not adaptable to changing demands. If a purpose of a building can’t be altered over time and instead must be torn down to create space for a new building, it leads to unnecessary waste of raw materials and energy.
Taking this into consideration in the early design phase and design multifunctional buildings that can be easily remodeled to serve a new purpose, we can avoid huge amounts of waste and CO2-emissions. Because only if a building is always in use, we make optimal use of the raw materials and energy that have been used in construction. Bear in mind that buildings made of concrete can stand up to a 100 years.
Green production
Locally sourced and produced
The way we produce is of course crucial when trying to cut our emissions. To begin with we always try to source and produce locally. Raw materials, such as ballast and binders, are sourced near our factories which in turn are strategically located close to the communities we help develop.
The precast production process makes it possible to optimize the use of raw materials, minimizing waste and energy used.
With a controlled industrial environment comes also benefits in quality control at every stage of the process. We can use better and higher-grade materials which results in better products and increased durability, creating more sustainable and long-lasting buildings.
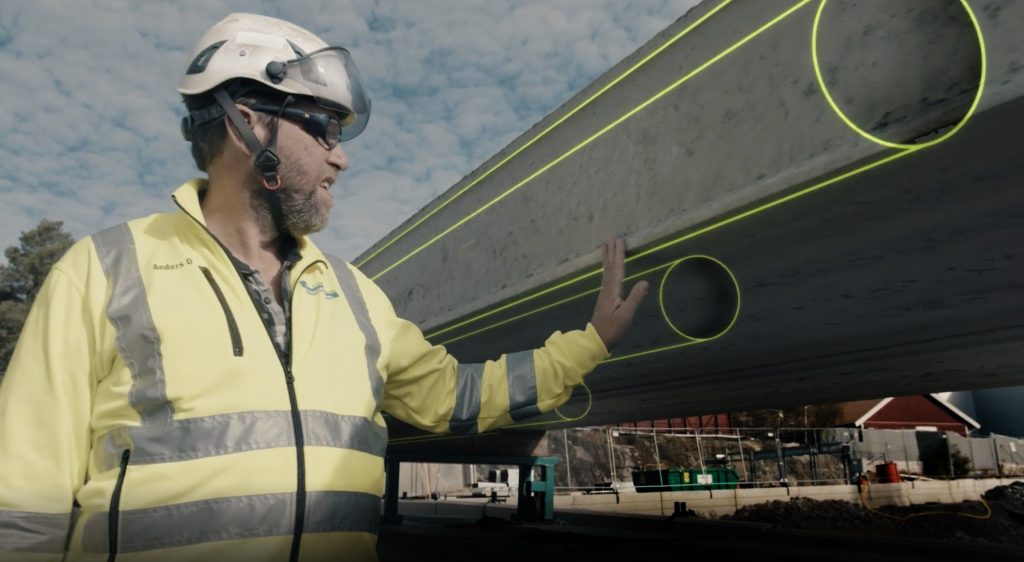
Less waste
With prefabricated structures and solutions, there is less material waste from the production facilities. Instead the waste can be reused. For example, crushed concrete is used to make new concrete for new frames, walls, and facades.
Our goal is to transform a majority of our production facilities into zero-waste facilities. Several of our production sites already have a closed circular production system, where all waste material is processed and reused.
Reusing and recycling
The more we can reuse and recycle, the better. For example, the hardened concrete waste from our production sites is crushed and reused for new concrete, the residue of fresh concrete is fully recycled and the waste steel goes back to the steel furnaces. Recycled coarse aggregate can form up to 20% of the total aggregate without any loss of quality.
Reusing elements
An exciting development is to design buildings in such a way, that the supporting structures are demountable at the end of a building’s life. As a result, it is possible to reuse elements as components in a new building. Opting for circularity by means of demountable construction is a major step forward from a sustainability point of view. Long-lasting design is always more sustainable than to tear down and start from scratch.
Green partnerships
To make a difference, we work closely together with our customers. Building strong, transparent, and holistic partnerships with all relevant stakeholders – customers, industry, governing agencies and science – makes it easier to come up with new, smart solutions to reduce the environmental impact. We aim to take the lead in this area and encourage everyone to follow.
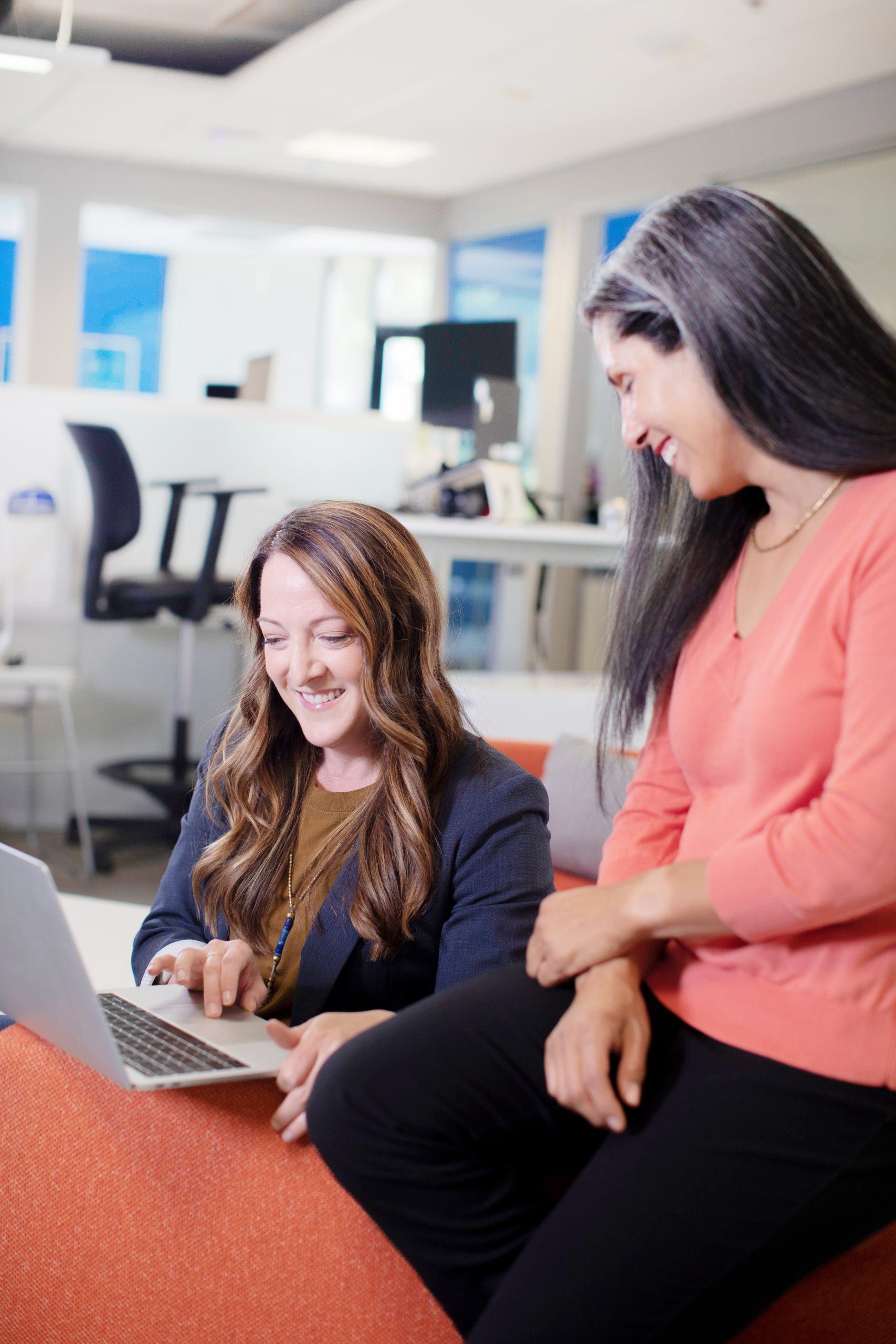
Customer partnership
We always strive for close customer partnerships which is also crucial from a sustainability standpoint. By putting great effort into the start-up phase when defining the project, close cooperation can make a huge difference. Here are a few examples of customer partnerships.
In Finland, our Green hollow cores help lower the CO2 -emission by 40% in a residential building project together with YIT.
In Sweden, we have been a part of creating Scandinavia’s first zero-energy hotel – Comfort Arena Hotel Arenastaden, Solna. Click to read more on this reference.
In the Netherlands we are one of the key-partners in a re-circular social housing project. The dwellings are designed for reassembly of the complete building with zero waste on site.
Industry partnership
Our industry is highly regulated, but to reach our sustainability goals, we have to push and develop the existing standards. We are working with the industry association to develop targets, standards and roadmaps that will be of concrete help in the green transition.